The aquaculture industry has experienced considerable growth in recent years, leading to an increased demand for efficient and cost-effective fish feed production. When selecting a fish feed processing line, it’s vital to strike a balance between cost-effectiveness, quality, and productivity to ensure long-term success. This article outlines the key considerations for choosing a fish feed processing line with a focus on cost-effectiveness.
Initial Investment vs. Long-Term Returns
When assessing the cost-effectiveness of a fish feed processing line, it is crucial to look beyond the initial purchase price and consider the long-term returns on investment:
- Equipment Lifespan: While higher-quality equipment may require a larger upfront investment, it often has a longer lifespan and lower maintenance needs, resulting in reduced long-term costs.
- Production Capacity: Ensure the processing line’s capacity meets both current and anticipated future needs. Overinvesting in capacity can unnecessarily tie up capital, whereas underinvesting may necessitate costly upgrades sooner than expected.
- Energy Efficiency: Although modern, energy-efficient equipment might have a higher initial cost, it can significantly decrease operational expenses over time.
Operational Costs
The daily operating costs of the fish feed processing line will greatly affect its overall cost-effectiveness:
- Energy Consumption: Compare the energy requirements of different processing lines. More energy-efficient models may have higher upfront costs but lower ongoing expenses.
- Water Usage: Some processing lines are more water-efficient than others, which can be a critical consideration in areas where water is limited or costly.
- Labor Requirements: Evaluate the level of automation and the number of operators needed. A more automated system might have higher initial costs but could lead to lower labor expenses over time.
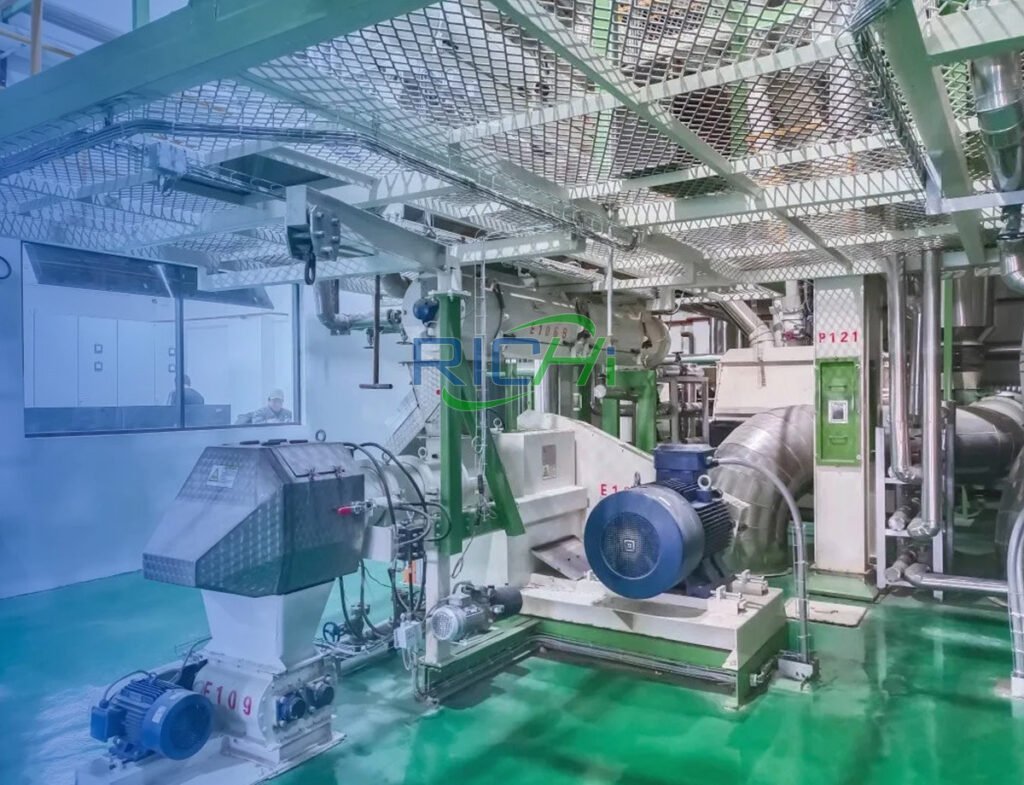
Raw Material Efficiency
The effectiveness of the processing line in converting raw materials into finished feed is a key factor in cost-effectiveness:
- Conversion Rates: Seek processing lines with high conversion rates to minimize waste and maximize the yield from raw materials.
- Flexibility in Ingredients: A processing line that can accommodate various ingredients allows for adaptation to fluctuating raw material prices, potentially reducing costs.
- Precision in Formulation: Advanced systems with precise ingredient dosing can optimize feed formulations, potentially lowering the usage of expensive ingredients.
Maintenance and Downtime
While regular maintenance is essential, excessive downtime can lead to significant costs:
- Maintenance Requirements: Compare the maintenance schedules and associated costs for different processing lines. Some may require more frequent or specialized maintenance.
- Spare Parts Availability: Evaluate the availability and cost of spare parts. Equipment from well-established manufacturers typically has better spare part availability.
- Technical Support: Assess the level and cost of technical support offered by the manufacturer. Timely and effective support can help minimize costly downtime.
Scalability and Flexibility
As your business grows or market demands change, the ability to adapt your fish feed production line is crucial for cost-effectiveness:
- Modular Design: Look for processing lines with modular designs that allow for easy expansion or reconfiguration.
- Product Versatility: A line capable of producing various types of fish feed (e.g., different pellet sizes, floating and sinking feed) offers flexibility to meet evolving market demands without additional investments.
Quality Control and Consistency
Producing high-quality, consistent feed is essential for maintaining customer satisfaction and avoiding costly product recalls:
- Quality Control Features: Advanced quality control systems may increase initial costs but can prevent expensive quality issues.
- Consistency in Production: Choose processing lines known for producing consistent feed, as this can reduce waste and improve feed conversion rates in fish farming.
Environmental Compliance
Environmental regulations can have a substantial impact on operational costs:
- Emissions Control: Processing lines with superior emissions control may have higher initial costs but can save on potential fines or retrofitting expenses in the future.
- Waste Management: Consider how different processing lines manage waste. More efficient waste management can lower disposal costs and possibly create additional revenue streams (e.g., selling by-products).
Training and Skill Requirements
The complexity of the processing line affects training expenses and the skill level required for operators:
- User-Friendly Interfaces: Processing lines with intuitive controls and user-friendly interfaces can reduce training time and costs.
- Automation Level: While highly automated systems may have higher upfront costs, they can lower the need for skilled operators, potentially reducing long-term labor expenses.
Financing Options
The availability and terms of financing can significantly influence the overall cost-effectiveness of your investment:
- Leasing vs. Purchasing: Compare the long-term costs of leasing versus purchasing the processing line.
- Manufacturer Financing: Some equipment manufacturers offer financing options that may be more favorable than third-party financing.
Local Factors
Consider local factors that may impact the cost-effectiveness of your chosen processing line:
- Electricity Costs: In regions with high electricity costs, energy efficiency becomes even more critical.
- Labor Costs: In areas with elevated labor costs, more automated systems may be more cost-effective.
- Raw Material Availability: Select a processing line that can efficiently utilize locally available raw materials.
Case Study: Comparing Two Fish Feed Processing Lines
To illustrate these considerations, let’s compare two hypothetical fish feed processing lines:
- Line A:
- Higher initial cost ($500,000)
- More energy-efficient (20% lower energy consumption)
- Requires only 2 operators due to a higher automation level
- Features advanced quality control systems
- Modular design for easy expansion
- Line B:
- Lower initial cost ($350,000)
- Standard energy efficiency
- Requires 4 operators
- Basic quality control features
- Fixed design
While Line B has a lower upfront cost, a five-year cost analysis might reveal that Line A is ultimately more cost-effective due to its lower energy and labor costs, reduced waste from superior quality control, and the ability to expand production easily as demand increases.
Conclusion
Selecting a cost-effective fish feed processing line necessitates careful evaluation of both short-term and long-term factors. While the initial investment is significant, it is essential to assess operational costs, efficiency, flexibility, and quality control capabilities. By adopting a comprehensive approach to cost-effectiveness, you can choose a processing line that not only fits your current budget but also aligns with your long-term business objectives in the competitive aquaculture sector. Remember, the least expensive option upfront may not always be the most cost-effective in the long run.
For details please contact: pellet line for sale
WhatsApp:86 138 3838 9622
Email:enquiry@richipelletmachine.com